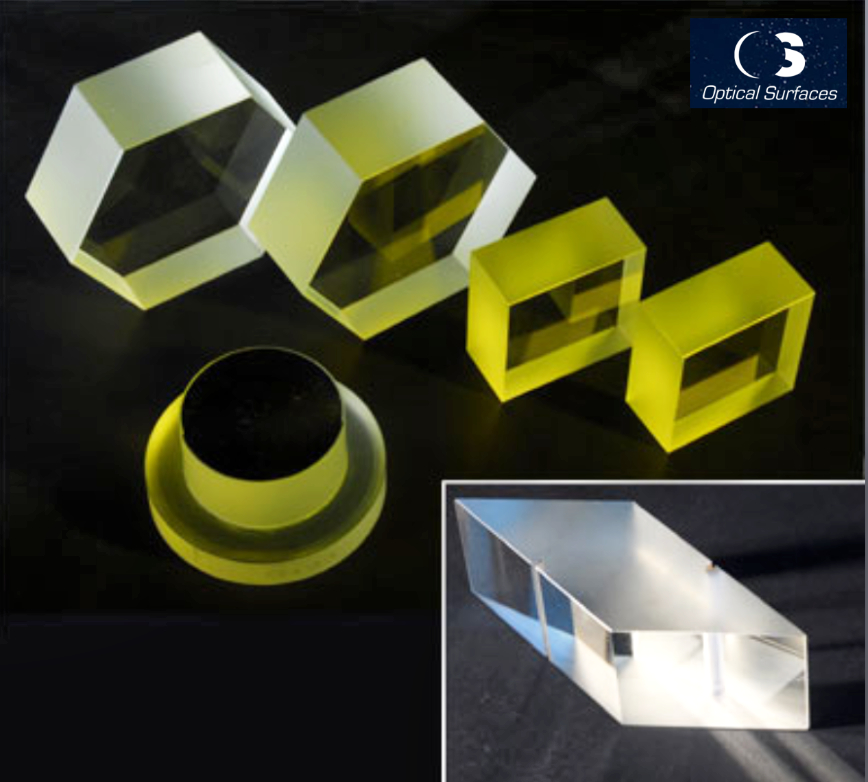
Dichroic beamsplitters from Optical Surfaces Ltd. are commonly used as light guiding optics in telescope spectrographs and to enable multichannel CCD cameras to simultaneously acquire images in different colors — beamsplitters operate by dividing an incident beam of light into two parts.
One part is transmitted through the beamsplitter, the other is reflected. In a dichroic beamsplitter the light is either reflected or transmitted based on wavelength. By varying the coating on a dichroic beamsplitter you can change the reflection to transmission ratio at specific wavelengths.
Dr. Aris Kouris, Sales Director at Optical Surfaces Ltd., said, “We are internationally recognised as a leading provider of high precision optical components for terrestrial and spaceborne telescope spectrographs. Spectrographs are the ‘go to’ scientific instruments used to study the chemical / physical conditions that exist through a cross-section of space. Combined with a terrestrial or spaceborne telescope a spectrograph can reveal the details that are stored in the spectral distribution of light from a distant star or galaxy. To achieve state-of-the-art image quality from telescope spectrographs it is essential to be able to produce dichroic beamsplitters with minimal flatness error and wavefront error both before and after coating. Operating in a uniquely stable manufacturing environment our team of experienced optical craftsmen routinely produce an ultra-high precision finish on all surfaces of beamsplitter blanks up to 500mm in diameter. Typical beamsplitters are manufactured to a surface accuracy of lambda/20 p-v at 633 nm, a surface quality of 10/5 and microroughness of less than 1 nm rms. Our dichroic beamsplitters can be supplied with an extensive range of coatings designed to operate at the required angle of incidence. Using proprietary techniques, we can correct for coating induced distortion.”
About Optical Surfaces
The company has been producing optical components and systems for astronomical and space research for nearly 60 years. The company’s ISO 9001-2015 approved manufacturing workshops and test facilities are deep underground in a series of tunnels excavated in solid chalk where temperature remains constant, and vibration is practically non-existent. With such stable conditions testing, particularly with long path lengths, becomes quantifiable and reliable.